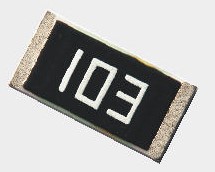
以低熔点合金焊接原理为基础,介绍了全自动共晶贴片机设备,对共晶焊接热台气氛保护进行了流体相关精度。通过对共晶焊接后焊接效果质检以及精度测量结果分析,工艺试验达到预期的效果,满足了目前产品市场化指标。研究结论对于提高
伴随着5G应用的快速地发展,更大的传输容量和更快的传输速率支撑成为光器件模块及光通讯行业的追求目标,光器件可以说是光通讯的命脉,而光芯片则为光模块的关键[1]。表面贴装技术是微电子元器件封装工艺中最重要的一道工序,封装测试是微电子成品走向市场化的最后一个环节[2]。因此表面贴装技术在微电子封装工艺流程中占有很重要的地位,多芯片共晶贴片就是这里面一种最重要的工艺环节。多芯片共晶贴片工艺直接决定着产品的质量及常规使用的寿命等,对产品性能指标有很大的影响。
共晶焊接又被称为低熔点合金焊接。共晶焊接的焊接过程是指在一定的温度和一定的压力下,将芯片在镀金的底座上轻轻摩擦,擦去界面不稳定的氧化层,使接触表面之间熔化,由二者固相形成一个液相[3]。冷却后,当温度不高于共熔点时,由液相形成的晶粒互相结合成机械混合物。
共晶合金技术在电子封装行业得到普遍的应用,如芯片与基板的粘接、基板与管壳的粘接等[4]。具有热导率高、电阻小、可靠性高、粘结后剪切力大和散热性好的优点[5-6]。对于散热性要求比较高的电子元器件大多会采用共晶合金来完成共晶焊接。
采用全自动共晶贴片设备做工艺贴装试验。设备是采用凸轮驱动、连杆联动、精密齿轮齿条、直线电机高精度模组和导轨,配合多轴运动控制技术和多相机视觉定位技术,确保设备持续高速、高精度运行。其原理是基于氮气气氛保护状态下,利用脉冲电源的加热功能,实现加热温度及加热时间实时可控,从而完成热沉垫块及焊料在管座上的一次性共晶焊接。该设备实现了多芯片共晶焊接的复杂工艺,实现了温度时间实时可控,还完全替代了手动焊料的过程,提高了多芯片共晶行业的智能化。同时高速、高精度运行不仅提高了生产效率,还降低了产品虚焊的可能性,使成品的一致性有了很大的提高。全自动共晶贴片设备结构如图1所示,多芯片共晶贴片工艺流程如图2所示。
本设备晶焊接热台采用脉冲加热方式,即利用脉冲电流通过高电阻率材料时产生的焦耳热来达到快速加热的效果。脉冲加热属于瞬时加热方式,只在融化焊料时进行通电加热,可根据焊料的不同设置多段温度曲线,实现加热温度及加热时间的实时控制,可满足多芯片共晶工艺。热台上连接有热电偶,用于实时反馈热台温度至温控系统,使热台温度与设置温度保持一致。
因在共晶热台处需要完成多个复杂的贴片过程,导致其不可能拥有一个稳定的气氛保护焊接环境,这直接引发了焊接时候焊料必须在大气环境中完成焊接,存在氧化的风险,同时焊料爬锡效果不好。针对焊接效果不好这样的一个问题,设计一个相对密闭的空间,同时持续充入氮气,控制流速使热台管座固定处形成一个相对来说比较稳定的气氛保护自然环境。三维模型经过结构简化后,采用仿真软件对简化后的共晶热台进行流体仿真分析。单一侧进气流体仿线所示,双侧进气流体仿线所示。
通过对仿真结果云图的分析可知,单一侧进气热台罩里边的氮气分布不均,热台管座共晶焊接时候左右两侧引线柱处的氮气流量也差别较大,整体的气氛环境不太理想,影响共晶焊接效果,通过后续试验也得出相同的结论,焊接效果不好。双侧进气仿真结果云图分析可知,热台罩里边各处分布相对均匀,热台管座共晶焊接时候左右两侧引线柱处的氮气流量基本没差别,左右两边同时共晶焊接时候能做到条件基本一致,焊接条件理想,后续工艺试验验证焊接效果达到客户使用要求。
5G技术的迅猛发展对激光器性能要求慢慢的升高,特别是随着传输速度提升,转换产生的热量也大幅度增多。为提升激光器本身散热能力,行业内设计出针对5G应用的新型号管座。通过增大管座扇形台、增大垫块尺寸、焊料直接焊接替代金丝键合等提升管座的散热能力。本次试验采用新型TO5605管座,与之匹配的垫块作为试验材料,焊料选用共晶行业普遍适用的金锡焊料(Au80Sn20)。
本次试验使用全自动共晶贴片机进行共晶焊接,测量仪器为二次元影像测量仪和显微镜。
管座上料方式为TO阵列料盘,并使用垫块蓝膜平台。焊接方法是在共晶台处将管座倒置夹紧固定后,首先将热沉垫块预焊在管座扇形台上,然后放置两块焊料,采取了特殊的运动机构将垫块和焊料置于扇形台固定位置,并通过吸嘴施加静压的方式,同时共晶,使垫块焊接在扇形台上。垫块电路与管腿焊接在一起,后续若需要焊接芯片可在热沉上直接完成,本次试验不焊接芯片。TO5605管座焊接如图5所示。
影响TO激光器多芯片共晶贴片工艺效果的因素主要有氮气气氛环境、氮气流量、共晶热台基础恒温、焊接共晶温度、焊料及管座清洁度、焊接压力、吸嘴拾放位置精度、吸嘴拾放旋转精度、相机校准精度、管座夹持一致性以及运动机构各个时序的配合。
的确定热沉和焊料吸嘴根据物料的尺寸大小以及管座尺寸选不一样规格型号的电木吸嘴,垫块吸嘴孔径为0.5 mm、焊料吸嘴孔径为0.2 mm。
本次试验在氮气气氛的保护下完成,通过设置不一样进气流量来确定最适合本次焊接的氮气流量,进气量高于7 ml/min时,吸嘴在放置垫块及焊料时会出现将垫块及焊料吹飞的情况,因此导致整个焊接失败。进气量低于5 ml/min时,因各个运动机构导致焊接环境无法封闭的情况,在氮气流量供应不足情况下,焊接后存在氧化的风险。所以最佳的氮气流量为5~7 ml/min,本次试验在6 ml/min的氮气保护氛围下完成焊接。
试验开始前给共晶热台设置一个基础恒温,保证完成管座预热,同时放置垫块和焊料时不可能会发生熔化现象,不会造成吸嘴的堵塞,因金锡焊料(Au80S20)的熔点为280℃,为避免焊料部分熔化以及吸嘴边粘上焊料情况出现,本次试验将恒温温度设置为270℃。
通过设置不一样梯度共晶温度段做试验来确定适合TO5605管座的最佳共晶温度,发现不一样的温度存在四种情况:
在做试验之前对管座进行超声清洗,清洗后在全自动共晶贴片机上完成共品焊接试验。焊接成品通过显微镜观察分析可知,焊接表面十分光滑明亮,不存在氧化的不良情况,爬锡高度达到了引线以上。热沉下焊料溢料均匀,满足焊接要求。共晶焊接后通过显微镜观察到管脚与垫块焊接的侧视图如图6所示。共品焊接后通过显微镜观察到管脚与垫块焊接的正视图如图7所示。
采用二次元影像测量仪,抽检10个焊接后的管座垫块,进行X向精度、Y向精度以及垫块焊接后的旋转角度精度的测量,测量精度结果见表1。
通过对抽检管座精度测量结果分析可知,垫块焊接后X向精度在±10μm,Y向精度在±13μm内,旋转角度精度在±1°内,满足焊接试验要求,达到目前市场化量产要求,同时为后续芯片贴装提供了精度保障。
通过对全自动多芯片共晶贴片机以及TO管座工艺的分析研究,得到全自动多芯片共晶贴片机可通过脉冲加热方式实现多种
型号TO管座的自动共晶焊接。通过对共晶焊接热台气氛环境的流体仿真分析,双侧进气可保证TO管座热台焊接处气氛环境的稳定持续保护,对左右引线柱焊接的一致性提供有效保障。通过对焊接后TO管座显微镜下观察分析可知,焊接表面十分光滑明亮,不存在氧化不良问题,且爬锡高度达到了引线柱高度的四分之一,满足当前市场标准及要求。对焊接管座贴片X、Y向及角度精度测量,X、Y向精度均为±15μm,角度精度为±1°,满足当前光通讯行业市场化批量生产需求。从而对于提高5G芯片本身的质量和可靠性提供了有力保障,对推动半导体封装产业更加快速的发展提供了参考依据。
文章出处:【微信号:wc_ysj,微信公众号:旺材芯片】欢迎添加关注!文章转载请注明出处。
非常少而获得更高的成品率。在巿场需求驱动下,裸片成本不断降低,尺寸越来越小。划缝宽度从100微米降到30微米,采
热特性分析中的应用,研究了中红外InAlAs/InGaAs/InP量子级联
,一般由GaAS、CdS、InP、ZnS等工作物质作为主要材料,制成半导体面结
驱动电流约150mA(偏置电流50mA,调制电流100mA);2、需对
之一摩尔曾在1965年作出预言:半导体将会得到快速地发展,电子学会随之获得广泛的普及,渗透到宽广的应用领域中。从半个世纪之后再往回看,这一预言早已得到了完美印证。虽然光纤
的发明颇具偶然性。1962年,休斯公司实验室研究人员伍德布利(Woodbury)等用液态硝基苯染料盒对红宝石
是一项无接触打标技术,在传统达标技术发展受到阻碍且展现出许多缺点的如今,瑞丰恒所掌握的紫外
代表他们陶瓷生产加工厂来到瑞丰恒调研参观,当他看到这款15W的高功率紫外
355nm目前,虽然疫情得到了某些特定的程度的控制,但一波又一波的疫情甚至新冠变株都仍然还在扰乱我们的生活。在医疗领域,新冠检
? /
瑞莎科技近日推出Radxa Rock 5C/Rock 5C Lite开发板
【Vision Board创客营连载体验】RT-Thread 之wifi连网