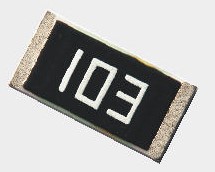
近二十年来,电子工业以惊人的速度发展。新技术的进步在减小设备尺寸的同时,也加大了分立元件制造商开发理想性能器件的压力。
在这些器件中,晶片电阻当前从始至终保持很高的需求,并且是许多电路的基础构件。它们的空间利用率优于分立式封装电阻,减少了组装前期准备的工作量。随着应用的普及,晶片电阻具有逐渐重要的作用。主要参数包括ESD保护、热电动势(EMF)、电阻热系数(TCR)、自热性、长期稳定性、功率系数和噪声等。
以下技术对比中将讨论线绕电阻在精密电路中的应用。不过请注意,线绕电阻没有晶片型,因此,受重量和尺寸限制需要采用精密晶片电阻的应用不使用这种电阻。
尽管升级每个组件或子系统能大大的提升整体性能,但整体性能仍是由组件链中的短板决定的。系统中的每个组件都具有关系到整体性能的内在优缺点,特别是短期和长期稳定性、频响和噪声等问题。分立式电阻行业在线绕电阻、厚膜电阻、薄膜电阻和金属箔电阻技术方面取得了进步,而从单位性能成本考虑,每种电阻都有许多需要加以权衡的因素。
各种电阻技术的优缺点如表1所示,表中给出了热应力和机械应力对电阻电气特性的影响。
应力(无论机械应力还是热应力)会造成电阻电气参数改变。当形状、长度、几何结构、配置或模块化结构受机械或别的方面因素影响发生明显的变化时,电气参数也会发生明显的变化,这种变化可用基本方程式来表示:R=ρL/A,式中
电流通过电阻元件时产生热量,热反应会使器件的每种材料发生膨胀或收缩机械变化。环境和温度条件也会产生同样的结果。因此,理想的电阻元件应可以依据这些自然现象进行自我平衡,在电阻工艺流程中保持物理一致性,使用的过程中不必进行热效应或应力效应补偿,来提升系统稳定性。
线绕电阻大体上分为“功率线绕电阻”和“精密线绕电阻”。功率线绕电阻使用的过程中会发生很大变化,不适于精密度要求很高的情况下使用。因此,本讨论不考虑这种电阻。
线绕电阻的制作的过程一般是将绝缘电阻丝缠绕在特定直径的线轴上。不同线径、长度和合金材料能够达到所需电阻和初始特性。精密线绕电阻ESD稳定性更高,噪声低于薄膜或厚膜电阻。线绕电阻还具有TCR低、稳定性高的特点。
线绕电阻初始误差可以低至±0.005%。TCR(温度每变化一摄氏度,电阻的变化量)能够达到3ppm/°C典型值。不过,降低电阻值,线ppm/°C。热噪声降低,TCR在限定温度范围内能够达到±2ppm/°C。
线绕电阻工艺流程中,电阻丝内表面(靠近线轴一侧)收缩,而外表面拉伸。这道工艺产生永久变形—相对于弹性变形或可逆变形,必须对电阻丝进行退火。永久性机械变化(不可预测)会造成电阻丝和电阻电气参数任意变化。因此,电阻元件电性能参数存在很大的不确定性。
由于线圈结构,线绕电阻成为电感器,圈数附近会产生线圈间电容。为提高使用中的响应速度,能够使用特殊工艺降低电感。不过,这会增加成本,而且降低电感的效果有限。由于设计中存在的电感和电容,线绕电阻高频特性差,特别是50kHz以上频率。
两个额定电阻值相同的线绕电阻,彼此之间很难保证特定温度范围内精确的一致性,电阻值不同,或尺寸不同时更为困难(例如,满足多种的功率要求)。这种难度会随着电阻值差异的增加进一步加剧。以1-kΩ电阻相对于100-kΩ电阻为例,这种不一致性是由于直径、长度,并有可能由于电阻丝使用的合金不同造成的。而且,电阻芯以及每英寸圈数也不同—机械特性对电气特性的影响也不一样。由于不同的电阻值具有不一样的热机特性,因此它们的工作稳定性不一样,设计的电阻比在设备生命周期中会发生很大变化。TCR特性和比率对于高精度电路极为重要。
传统线绕电阻加工方法不能消除缠绕、封装、插入和引线成型工艺中产生的各种应力。固定过程中,轴向引线往往采用拉紧工艺,通过机械力加压封装。这两种方法会改变电阻,无论加电或不加电。从长期角度看,由于电阻丝调整为新的形状,线绕元件会发生物理变化。
薄膜电阻由陶瓷基片上厚度为50Å至250Å的金属沉积层组成(采用真空或溅射工艺)。薄膜电阻单位面积阻值高于线绕电阻或BulkMetal®金属箔电阻,而且更为便宜。在需要高阻值而精度要求为中等水平时,薄膜电阻更为经济并节省空间。
它们具有最佳温度敏感沉积层厚度,但最佳薄膜厚度产生的电阻值严重限制了可能的电阻值范围。因此,采用各种沉积层厚度能轻松实现不同的电阻值范围。薄膜电阻的稳定性受温度上升的影响。薄膜电阻稳定性的老化过程因实现不同电阻值所需的薄膜厚度而不同,因此在整个电阻范围内是可变的。这种化学/机械老化还包括电阻合金的高温氧化。此外,改变最佳薄膜厚度还会极度影响TCR。由于较薄的沉积层更容易氧化,因此高阻值薄膜电阻退化率非常高。
由于金属量少,薄膜电阻在潮湿的条件下极易自蚀。浸入封装过程中,水蒸汽会带入杂质,产生的化学腐蚀会在低压直流应用几小时内造成薄膜电阻开路。改变最佳薄膜厚度会极度影响TCR。由于较薄的沉积层更容易氧化,因此高阻值薄膜电阻退化率非常高。
如前所述,受尺寸、体积和重量的影响,线绕电阻不可能采用晶片型。尽管精度低于线绕电阻,但由于具有更高的电阻密度(高阻值/小尺寸)且成本更低,厚膜电阻得到普遍使用。与薄膜电阻和金属箔电阻一样,厚膜电阻频响速度快,但在目前使用的电阻技术中,其噪声最高。虽然精度低于其他技术,但我们之所以在此讨论厚膜电阻技术,是由于其大范围的应用于几乎每一种电路,包括高精密电路中精度要求不高的部分。
厚膜电阻依靠玻璃基体中粒子间的接触形成电阻。这些触点构成完整电阻,但工作中的热应变会中断接触。由于大部分情况下并联,厚膜电阻不会开路,但阻值会跟着时间和温度持续增加。因此,与其他电阻技术相比,厚膜电阻稳定性差(时间、温度和功率)。
由于结构中成串的电荷运动,粒状结构还会使厚膜电阻产生很高的噪声。给定尺寸下,电阻值越高,金属成份越少,噪声越高,稳定性越差。厚膜电阻结构中的玻璃成分在电阻工艺流程中形成玻璃相保护层,因此厚膜电阻的抗湿性高于薄膜电阻。
将具有已知和可控特性的特种金属箔片敷在特殊陶瓷基片上,形成热机平衡力对于电阻成型是十分重要的。然后,采用超精密工艺光刻电阻电路。这种工艺将低TCR、长期稳定性、无感抗、无ESD感应、低电容、快速耐热性和低噪声等重要特性结合在一种电阻技术中。
这些功能有助于提高系统稳定性和可靠性,精度、稳定性和速度之间不必相互妥协。为获得精确电阻值,大金属箔晶片电阻可通过有选择地消除内在“短板”进行修整。当需要按已知增量加大电阻时,可以切割标记的区域(图2),逐步少量提高电阻。
合金特性及其与基片之间的热机平衡力形成的标准温度系数,在0°C至+60°C范围内为±1ppm/°C(Z箔为0.05ppm/°C)(图3)。
采用平箔时,并联电路设计可降低阻抗,电阻最大总阻抗为0.08uH。最大电容为0.05pF。1-kΩ电阻设置时间在100MHZ以下小于1ns。上升时间取决于电阻值,但较高和较低电阻值相对于中间值仅略有下降。没有振铃噪声对于高速切换电路是十分重要的,例如信号转换。
100MHZ频率下,1-kΩ大金属箔电阻直流电阻与其交流电阻的对比可用以下公式表示:
金属箔技术全面组合了高度理想的、过去达不到的电阻特性,包括低温度系数(0°C至+60°C为0.05ppm/°C),误差达到±0.005%(采用密封时低至±0.001%),负载寿命稳定性在70°C,额定加电2000小时的情况下达到±0.005%(50ppm),电阻间一致性在0°C至+60°C时为0.1ppm/°C,抗ESD高达25kV。
当然并非每位设计师的电路都需要全部高性能参数。技术规格相当差的电阻一样能用于大量应用中,这方面的问题分为四类:
(4)有目的地提前计划使用精密电阻满足今后升级要求(例如,利用电阻而不是有源器件保持电路精度,从而节省成本,否则仅仅为了略微提高性能则要明显地增加成本)。
例如,在第二(2)类情况下,一个参数必须根据所有参数的经济性加以权衡。与采用全面优异性能的电阻相比,这样做才能够节省成本,因为不需要调整电路(及组装相关组件的成本)。主要通过电阻而不是有源器件提高精度也能节约成本,因为有源器件略微提高一点性能所需的成本要比电阻高的多。另一个问题是:“利用高性能电阻提高设备性能是不是能够提高市场的市场占有率?”